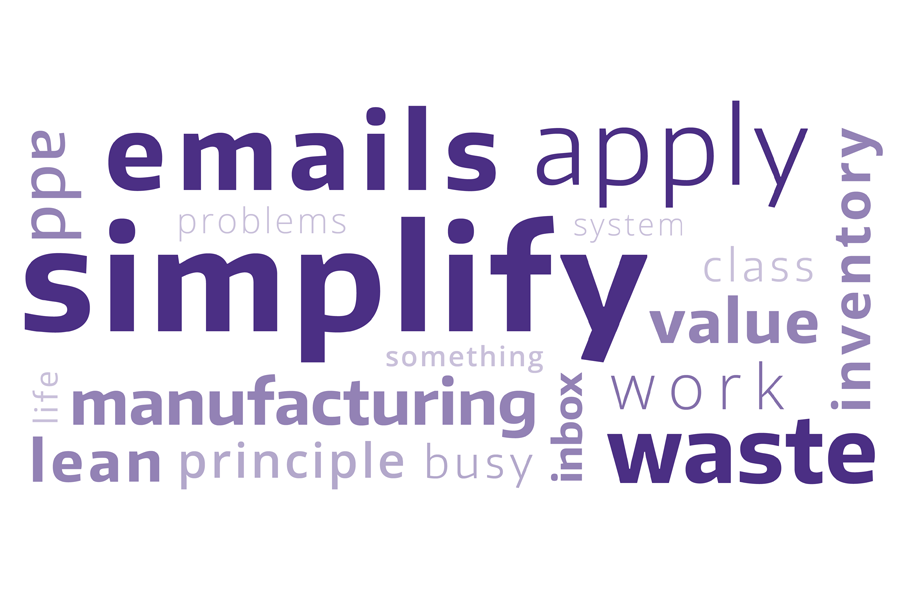
Using Lean Manufacturing Principles to Simplify Life
Simplify. I don’t know how many times my husband has used this word over the years. Any time I complain or struggle with something, his answer is the same.
There’s too much to do! Simplify.
I’m running late! Simplify.
I can’t find my keys! Simplify.
How could simplify be the answer to so many of my crises, small and big? Because my husband, Michael R. Wagner, is an assistant professor of Operations Management at the Foster School of Business, and he happens to know a thing or two about efficiency.
To simplify means to make less complex or complicated. Complex processes typically have a lot of waste, so simplifying a process will reduce waste, improving efficiency.
In his operations management class, Michael teaches his students about lean manufacturing, a systematic method to eliminate waste within a manufacturing system. Lean doesn’t only apply to businesses, but can apply to everyday processes. Michael integrates these concepts into his everyday life, and tries to integrate them into mine.
“The Toyota Production System,” a manufacturing methodology developed over decades by Toyota of Japan, is the precursor of lean manufacturing. The system “identifies three classes of waste, “ Michael says. “In Japanese they are called muda, muri, and mura.”
Muda is anything that doesn’t add value. “To reach our goals we must focus on doing the things that actually add value for us – every time you do something, think to yourself: ‘Why am I doing this?’” Michael suggests. “If what you are doing doesn’t add value, stop doing it.”
An example: Spending hours on social media, even though you get no value from it. Solution: Limit your use.
A form of muda is excess inventory, which hides problems. When we have too much stuff, we either get so accustomed to it that we don’t see problems or we don’t know where to start to fix them.
When your desktop is cluttered, it might take you forever to find a document. When the fridge is full or the pantry cluttered, food will go to waste.
“A good rule is to try to reduce excess inventory,” says Michael. “I always strive to attain ‘inbox zero,’ and I have nothing saved on my desktop.”
Also try to minimize work in progress inventory, which are partly finished goods at various stages of the production process. An example of a partly finished good is laundry sitting in the dryer.
“Clothes and linens have zero value sitting in the dryer, not to mention they get wrinkly. So when I do laundry, I make sure I have enough time to do it from start to finish. This way I don’t have to go hunting for clean socks, which saves me time and effort as well.”
Point-of-use storage is another lean manufacturing principle that can be applied to everyday life. It means that every part needed to do a job is stored in the area that uses it. This reduces search time and unnecessary travel.
“I use my in-office printer rather than the departmental printer, which is a three minute walk away,” Mike explains. “When I need to print a lot, those three minute trips add up.”
Michael swears this is not a sign of laziness. In fact, he says taking a walk or a break is not considered unnecessary movement because it adds value. The key is to take a walk when you want to or need to, not while you are in the middle of some work.
“A great place where you can apply this concept is the kitchen, so that you can make the cooking flow easier,” he says. “If you prepare your plates next to the stove, store the plates next to it. If you mix your ingredients next to the sink, store your ingredients next to it.”
A second class of waste is muri – overburden, doing things that are beyond one’s power. “Don’t take on more than you can chew, don’t overcommit yourself. During a busy week, drop off your laundry at the cleaners to free up some time. Outsource,” Michael recommends.
The third class of waste is mura – unevenness. “Avoid large swings in your workload – so again don’t be afraid to outsource if you are particularly busy. Don’t procrastinate. Delaying and putting off tasks and errands creates unevenness as you are left having to do everything at the last minute.”
This all makes sense in theory, but how do you find opportunities to simplify in your own life? A useful concept is the Five Whys. The goal of this technique is to determine the root cause by repeating the question “Why?” five times. Each question forms the basis of the next one.
A few years ago, I forgot to pay a bill and he called this a “defect” in a process. He proceeded to apply the five whys:
I forgot to pay my bill.
Why?
I never saw the email for it.
Why?
I guess I must have missed it.
Why?
It must have gotten lost among my other emails.
Why?
Because I have 1,000 emails in my inbox.
Why?
Because I don’t take the time to either delete or file away the email.
So the solution to the problem? Try to attain “inbox zero” by minimizing the number of emails in your inbox that require your attention. Remember, high inventory hides problems, and in this case the high volume of emails hid the email about the unpaid bill.
Applying lean principles to your life will take work up front, but the rewards will be long lasting. You’ll have more time for what you truly enjoy. That’s why there’s one particular principle that my husband absolutely lives by: Kaizen (“continuous improvement”). “Never be satisfied,” Michael says. “You can always do something better and there is always room for improvement. Getting things done is not about working harder, but working smarter.”